Electric motors are renowned for their lightweight design, compactness, and durability, making them essential in converting electrical energy into mechanical energy. They are widely used across various industrial and economic sectors, from manufacturing plants to household appliances. However, like any mechanical device, electric motors can experience malfunctions. Understanding these common faults, their consequences, and the methods for diagnosing them is vital for ensuring optimal performance and extending the lifespan of these critical devices. The Ghaima Group is a leader in diagnosing and repairing such malfunctions, ensuring motors remain efficient and reliable.
Common Faults in Electric Motors
Interturn Closure
Interturn closure occurs when the insulation within a single winding deteriorates. This deterioration can result from various factors such as excessive heat, vibration, or electrical stress. When insulation fails, it can cause short circuits between the turns of a winding, leading to inefficient motor performance and increased electrical losses. Over time, this can escalate into more severe damage, potentially rendering the motor inoperable.
Winding Break
A winding break is analogous to a phase loss in the motor’s operation. If a winding break occurs while the motor is running, it suddenly loses power and begins to overheat. This overheating is due to the imbalance in the motor’s electrical circuit, which can cause excessive current in the remaining windings. Prompt detection and repair are essential to prevent further damage to the motor and associated equipment.
Wear and Friction in Bearings
Bearings are critical components that ensure smooth rotation of the motor shaft. Over time, bearings can wear out or become damaged due to friction, contamination, or lack of lubrication. Symptoms of bearing wear include increased mechanical vibration and noise during operation. If not addressed, worn bearings can lead to significant overheating, reduced performance, and eventually, complete motor failure. Replacing the bearings at the first sign of wear can prevent these issues.
Engagement of the Rotor with the Stator
Engagement of the rotor with the stator is typically a consequence of mechanical failure in the bearings, their seats, or the motor housing. When the rotor comes into contact with the stator, it can cause severe mechanical damage, including scoring or rubbing of the rotor surface and stator laminations. This not only affects motor efficiency but can also lead to catastrophic failure if left unchecked.
Damage to the Motor Housing
Motor housing damage can occur due to a variety of reasons, such as physical shocks, excessive loads, improper mounting, or poor-quality materials. A compromised motor housing can affect the alignment and stability of the internal components, leading to operational issues and increased risk of motor failure. Regular inspection and maintenance are necessary to identify and rectify housing damage before it leads to more significant problems.
Rotor Imbalance
Rotor imbalance is caused by uneven wear of the motor’s working components, changes in the fit of the disks, or loosening of the parts that make up the rotor. This imbalance can result in increased vibration, which not only affects the motor’s performance but can also cause damage to other mechanical components. Ensuring that the rotor is balanced and properly maintained is crucial for smooth and efficient motor operation.
Blower Impeller Malfunction
The blower impeller is responsible for cooling the motor by circulating air. If the impeller becomes deformed or accidentally turns over, the motor will continue to operate but will overheat quickly. This overheating can significantly shorten the motor’s service life and lead to premature failure. Regular inspection and maintenance of the blower impeller are essential to ensure proper cooling and prevent overheating.
Consequences of Motor Malfunctions
Engine Overheating
Overheating is a common consequence of various motor malfunctions. When a motor overheats, it can damage the windings and housing, leading to reduced equipment performance and potentially rendering the motor unusable. Overheating can also affect other components connected to the motor, causing further operational issues.
Electrical Short Circuit
In the absence of proper electrical protection, motor malfunctions can lead to short circuits. A short circuit occurs when electrical current takes an unintended path, potentially causing sparks, fire, and severe damage to the motor and surrounding equipment. Implementing adequate electrical protection measures is critical to prevent such hazardous incidents.
Mechanical Damage
Mechanical damage can result from increased vibration, shocks, and other factors associated with motor malfunctions. This damage can affect the motor’s structural integrity and overall functionality, leading to costly repairs or replacements. Regular maintenance and timely intervention are essential to mitigate mechanical damage.
Equipment Downtime
Motor failures can cause significant production stoppages, leading to equipment downtime and loss of revenue. In industrial settings, where motors play a crucial role in continuous operations, unexpected downtime can have severe financial implications. Ensuring the reliability and efficiency of electric motors is vital for maintaining uninterrupted production processes.
Diagnostic Methods for Electric Motors
Vibration Diagnostics
Vibration diagnostics involve measuring and analyzing vibration parameters such as displacement, acceleration, and velocity. These measurements help detect early signs of mechanical issues, such as imbalance, misalignment, or bearing wear. Vibration analysis is a powerful tool for identifying potential problems before they escalate into major failures.
Thermal Imaging Diagnostics
Thermal imaging diagnostics use infrared cameras to detect temperature variations in motor components. This method allows for the identification of defects in bearings, contact connections, cooling systems, stator windings, and other critical parts. By visualizing heat patterns, thermal imaging helps pinpoint areas of concern that may require maintenance or repair.
Insulation Condition Diagnostics
Insulation condition diagnostics focus on assessing the integrity of the motor’s insulation system. Insulation damage is often caused by elevated temperatures, vibrations, and machine overloads. Techniques such as insulation resistance testing and polarization index measurement help evaluate the health of the insulation and identify potential issues that could lead to failure.
Analysis of Electric Motor Parameters
Analyzing electric motor parameters involves monitoring various operational metrics to detect faults. This approach can identify a wide range of issues, including bearing damage, eccentricity, rotor damage, shaft misalignment, and interturn short circuits. Continuous monitoring of motor parameters provides valuable insights into its condition and helps prevent unexpected failures.
Application of Artificial Neural Networks
Artificial neural networks (ANNs) can analyze measured parameters of the electric motor to determine its current state based on previously known classes of technical conditions. ANNs can process vast amounts of data and identify patterns that indicate potential faults. This advanced diagnostic method offers a sophisticated approach to motor condition monitoring and fault detection.
Professional Electric Motor Diagnostics
Electric motor diagnostics require specialized skills and tools, making it a task best entrusted to professionals. In Dubai, the Ghaima Group of Companies is a leader in the maintenance and repair of electrical equipment. Their expertise ensures accurate diagnostics and effective solutions, helping to maintain the efficiency and reliability of electric motors in various applications.
Conclusion
Electric motors play a vital role in modern industry and everyday life, but their reliability can be compromised by various faults. Understanding common motor malfunctions, their consequences, and the diagnostic methods available is crucial for maintaining optimal performance and longevity. Regular maintenance, timely intervention, and professional diagnostics are key to preventing motor failures and ensuring the smooth operation of equipment. With the right care and attention, electric motors can continue to provide the reliable performance that industries and economies depend on.
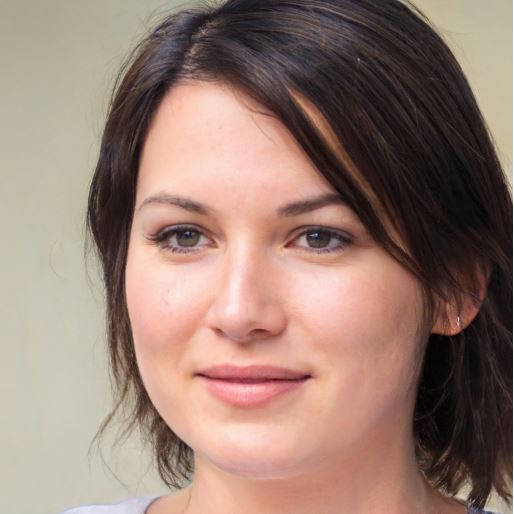
Basketball fan, father of 3, music blogger, Mad Men fan and storyteller. Producing at the crossroads of simplicity and intellectual purity to craft an inspiring, compelling and authentic brand narrative.